FGB Bearings : Spherical plain bearings | Ball bearings | Roller bearings
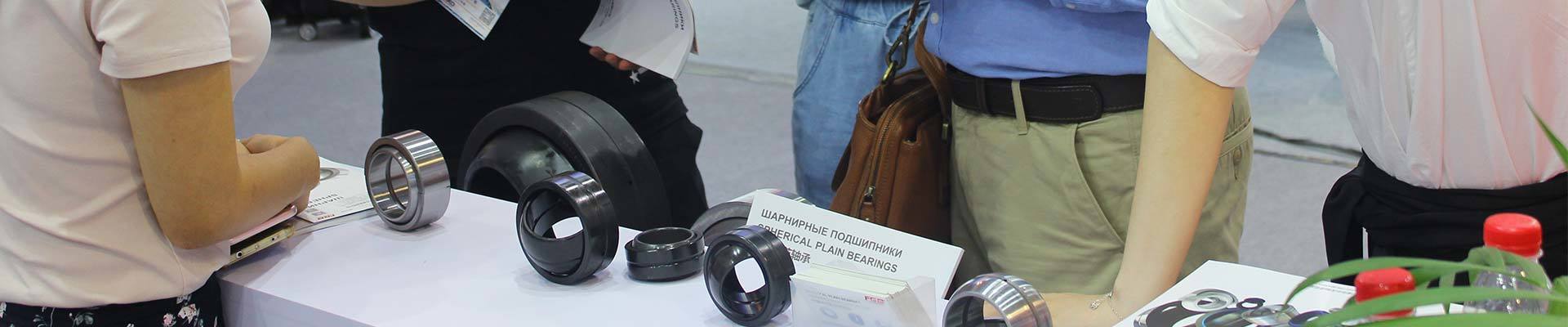
22
2025
-
05
Exploring the Versatility of Articular Balls in Various Industrial Applications
Exploring the Versatility of Articular Balls in Various Industrial Applications
Table of Contents
- 1. Introduction to Articular Balls
- 2. What Are Articular Balls?
- 3. Types of Articular Balls Used in Industry
- 4. Applications of Articular Balls in Various Industries
- 4.1 Articular Balls in the Automotive Industry
- 4.2 Articular Balls in Manufacturing
- 4.3 Articular Balls in Aerospace
- 4.4 Articular Balls in Robotics
- 4.5 Articular Balls in Medical Devices
- 5. Benefits of Using Articular Balls in Industrial Applications
- 6. Challenges in Using Articular Balls and Solutions
- 7. Future Trends in Articular Balls Technology
- 8. Conclusion
- 9. FAQs
1. Introduction to Articular Balls
In the vast realm of industrial components, **articular balls** stand out due to their unique versatility and functional significance. These specially designed components serve as critical connectors in various machinery, enabling smooth movement and minimizing wear and tear. In this article, we will explore the numerous applications of articular balls, their types, and their benefits across different industries.
2. What Are Articular Balls?
Articular balls are spherical connectors utilized in mechanical systems to facilitate rotational movement and load distribution. Often made from robust materials such as steel, plastic, or ceramics, these components are engineered to withstand high pressures and extreme temperatures. Their primary function is to provide a pivot point, allowing for greater flexibility and efficiency in machinery and equipment.
3. Types of Articular Balls Used in Industry
Understanding the different types of articular balls is crucial for selecting the right component for specific applications. Here are some of the most common types:
3.1 Standard Articular Balls
These are the basic variants, typically used in general applications where moderate loads and speeds are involved. They are an economical choice for many industries.
3.2 Heavy-Duty Articular Balls
Designed for high-load applications, heavy-duty articular balls are made from reinforced materials to handle significant stress without deformation.
3.3 Stainless Steel Articular Balls
Ideal for applications requiring corrosion resistance, stainless steel articular balls are often used in the food and medical industries, where hygiene is paramount.
3.4 Plastic Articular Balls
Lightweight and resistant to chemical corrosion, plastic articular balls are common in environments where metal components may degrade due to exposure to harsh chemicals.
3.5 Custom Articular Balls
For specialized applications, custom articular balls can be designed to meet unique specifications regarding size, material, and performance characteristics.
4. Applications of Articular Balls in Various Industries
Articular balls are indispensable across several industrial sectors. Below, we delve into some prominent applications.
4.1 Articular Balls in the Automotive Industry
In the automotive sector, articular balls are vital for steering and suspension systems. They allow for smooth steering adjustments and absorb shocks, enhancing vehicle stability and passenger comfort. Whether in power steering assemblies or suspension linkages, the reliability of articular balls directly impacts vehicle performance.
4.2 Articular Balls in Manufacturing
The manufacturing industry utilizes articular balls in various machinery and automation equipment. From conveyor systems to robotic arms, these components help ensure precise movement and positioning, which is crucial for maintaining production efficiency.
4.3 Articular Balls in Aerospace
In aerospace applications, articular balls are used in flight control systems and landing gear mechanisms. Their ability to perform under extreme conditions makes them essential for ensuring the safety and reliability of aircraft.
4.4 Articular Balls in Robotics
Robotic systems extensively employ articular balls to facilitate movement in joints and connections. They enable robots to perform complex tasks with agility and precision, proving critical in industries ranging from manufacturing to healthcare.
4.5 Articular Balls in Medical Devices
In the medical field, articular balls are found in devices such as prosthetics and surgical instruments. Their ability to provide smooth movement is vital for the functionality and effectiveness of these devices, enhancing patient care.
5. Benefits of Using Articular Balls in Industrial Applications
The advantages of incorporating articular balls into industrial applications are numerous:
5.1 Enhanced Mobility and Flexibility
Articular balls facilitate unrestricted movement, allowing machinery to operate more efficiently and with fewer restrictions.
5.2 Reduced Wear and Tear
By providing a smooth pivot point, articular balls minimize friction, which significantly reduces wear and tear on components, enhancing the lifespan of machinery.
5.3 Easy Installation and Maintenance
Articular balls are designed for straightforward installation, making them a convenient choice for engineers and technicians. Their maintenance requirements are also minimal, ensuring long-term reliability.
5.4 Versatility Across Applications
The diverse range of articular balls available means they can be tailored to suit various industrial needs, making them an adaptable component for different environments and applications.
5.5 Cost-Effectiveness
Given their durability and low maintenance needs, articular balls can be a cost-effective solution in the long run, reducing the need for frequent replacements.
6. Challenges in Using Articular Balls and Solutions
Despite their many benefits, the use of articular balls can present certain challenges.
6.1 Material Limitations
Not all materials meet the specific demands of every application. To address this, manufacturers are increasingly developing hybrid materials that combine the benefits of various substances, such as metal and plastic.
6.2 Precision Manufacturing
The need for high precision in manufacturing articular balls can be a hindrance. Investing in advanced manufacturing technologies, such as CNC machining, can enhance accuracy and quality.
6.3 Environmental Factors
Extreme temperatures and corrosive environments can affect the performance of articular balls. Selecting the appropriate materials and finishes can mitigate this issue, ensuring reliability under challenging conditions.
7. Future Trends in Articular Balls Technology
As industries evolve, so does the technology surrounding articular balls. Emerging trends include:
7.1 Smart Articular Balls
The integration of sensors into articular balls can provide real-time data on performance and wear, allowing for predictive maintenance and enhanced operational efficiency.
7.2 Sustainable Materials
With an increasing focus on sustainability, manufacturers are exploring eco-friendly materials to produce articular balls, contributing to reduced environmental impact.
7.3 Customization
The demand for customized solutions is on the rise. Future manufacturing processes will likely focus on increasing the ability to tailor articular balls to specific application requirements.
8. Conclusion
Articular balls play a pivotal role in various industrial applications, enhancing performance, reliability, and efficiency. Their versatility across sectors such as automotive, manufacturing, aerospace, robotics, and medical devices underscores their importance in modern machinery. As technology advances and industries evolve, the demand for high-quality, durable articular balls will continue to grow, driving innovation and improvement in their design and application.
9. FAQs
What are articular balls primarily used for?
Articular balls are primarily used to facilitate rotational movement and load distribution in mechanical systems across various industries.
How do articular balls improve machinery performance?
By minimizing friction and providing smooth movement, articular balls reduce wear and tear on components, enhancing overall machinery performance.
Can articular balls be customized for specific applications?
Yes, manufacturers can create custom articular balls to meet unique specifications, making them adaptable for various industrial needs.
What materials are commonly used to manufacture articular balls?
Articular balls are commonly made from materials such as steel, stainless steel, plastic, and ceramics, depending on the application requirements.
How do I select the right articular ball for my application?
Selecting the right articular ball involves considering factors such as load requirements, environmental conditions, and the specific movement needed for your machinery.